A Q&A with Pete Bremer, Assurant’s VP of Global Automation Engineering
The first time I met Pete Bremer, he was quoting Thanos, the supervillain from the Marvel Universe, and talking about a dry ice cleaning system his team created to return used mobile phones to a like-new shine. And, as crazy as it sounds to say about a process that uses frozen CO2 to remove debris, it was enthralling.
So I was shocked when Pete said he wanted AI and automation to become a mundane part of our overall operations – almost boring in their use case. Recently, I sat down with him to get more context around the use of AI and automation in Assurant’s device care centers, why it’s boring, and how it’s applied to the processes of repairing, replacing, and refurbishing more than 20M mobile devices every year.
Q: What do you mean when you say you want AI and automation to be boring?
When you think about the best possible applications of AI and automation, you think of manual, monotonous processes that can be improved. Examples of these processes include sorting and opening the thousands of packages shipped to our facilities every day, testing the functionality of used smart tech before refurbishing and reselling it or cleaning more than 20M mobile devices a year. And when you use AI and automation to improve these processes – whether you’re talking about increasing speed to market or driving more customizability – you’re basically creating programs and technology to do boring things faster and better.
There’s a cool factor to this, especially at the beginning. Watching a robot choose the right phone from your inventory to fulfill a customer order is cool the first couple of times. The same is true of creating logic that helps make decisions about when to repurpose a smartwatch and when to recycle it. But because these are processes that, at least in Assurant’s device care centers, need to happen thousands of times a day, the reality is they’re monotonous.
Like all monotonous tasks when they’re done right, they should be predictable. So developing AI models that improve the decision-making around device repair or repurposing and the automation to carry it out is cool at first but, because we’re doing it right, it’s boring in its predictability.
Q: How do new tech releases impact predictability? How can you standardize and automate processes that need to be flexible enough to adapt to new wearables, hearables, smartphone releases or other upgraded tech models?
This is definitely an area that uniquely impacts our industry. Let’s take the mobile market as an example. The big players like Apple, Samsung, and Google release new smartphone models every year. But consumers don’t all upgrade at once, which means you have a mix of legacy devices and new devices that need to be serviced. And a better question might be how you can afford not to automate processes with new tech hitting the market constantly. Humans can’t be expected to retain expertise on every model.
At Assurant, we’re creating programs that perform basic, device-agnostic tasks like device cleaning, charging, cosmetic grading, functional testing, and sorting. By breaking this down into step-by-step tasks, we’re able to address each task vs. each phone model and ensure that the automation systems and software we create will apply to the next models that hit the market.
If we’d started designing the process of refurbishing an iPhone 10 start-to-finish before looking at any other models, we’d have a system that works for iPhone 10. Instead, we’re designing a modular, task-based set of tools that can be joined together to fully automate device processing. So instead of designing all tasks around a particular phone model, we’re looking at each task and saying, “How can we automate each task to apply to every phone model?”
Q: What are some examples of this that you’ve brought to life so far?
Four things come to mind right away: (1) our C02-based cleaning system, (2) the proprietary Vision Tunnel cosmetic grading tech, (3) how we’re using robotics, and (4) the fully automated line.
C02-Based Cleaning System
One of the challenges in the electronics industry is the ability to quickly and efficiently clean used technology so that it can be repaired or refurbished and put back into market as soon as possible. We’ve identified an environmentally sustainable standard that takes a specialized organic approach to cleaning used technology. It uses dry ice — accelerated at high speeds — to create “micro impacts” on the surface of an object to safely remove unwanted damage or material. Having this system in place results in significant cost savings and increased production capacity.
Assurant Vision Tunnel technology
This is the brainchild of our software and physical automation team – with two of our mechatronics graduates from Middle Tennessee State University leading the charge – that built this game-changing technology right at our Tech Center. The move from manual inspections to automated cosmetic grading helps us achieve maximum production capacities while adhering to the highest quality standards.
With our automated visual inspection system — which runs on a combination of high-resolution cameras, specialized lighting, computer vision, machine learning, and proprietary software — we can visually analyze the conditions of any phone model and detect imperfections. This helps us achieve maximum production capacity, while ensuring regulatory compliance.
AI Robotics in Assurant Device Care Centers
We’re transforming logistics processes and warehousing with powerful robotics from our partner, Locus. Working alongside our team of dedicated associates, these robots are digitalizing manual logistics. This includes tasks like picking, packing, and returns in a streamlined way that minimizes errors and order processing times.
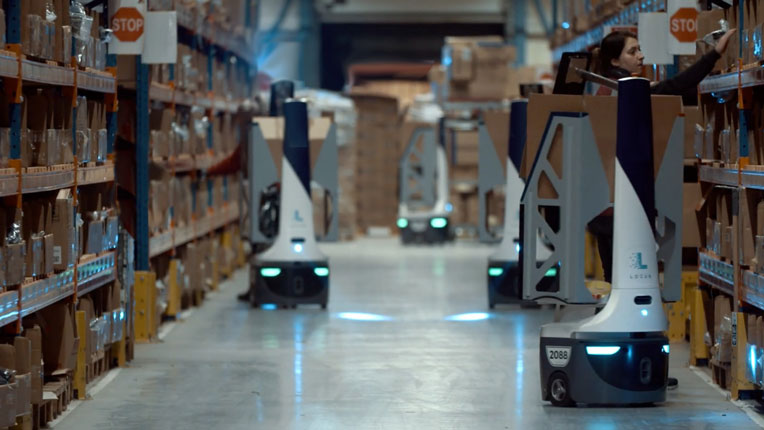
The Locus robots are powered by sophisticated algorithms, AI, and machine learning capabilities that analyze the data and help optimize our device care center layouts, inventory placement, and routing. We don’t have to choose between speed and accuracy because we have the best of both worlds in one efficient solution. And that helps us work smarter, not harder.
The Assurant Automated Line
Our Assurant Device Care Centers are only as good as the material handling technology and transport systems that keep it moving. Conveyor technology plays an essential role when it comes to the flow of materials in distribution and fulfillment centers. More important, this technology ensures that internal logistics processes run smoothly. I’m happy to report that later this year, we’re installing five fully automated lines that will integrate our existing technology models with a custom-fit conveyance system. This system will be used to move materials from one location to another and will also serve as a buffer for product flow. These implementation updates will alleviate our peak season demands and promote a safer and more stress-free environment for our associates.
Q: What’s next on the Assurant automation roadmap?
We want to keep evolving in terms of automation since it’s integral to advancing and growing our environment. It’s clear that automation enables our teams to be faster, more agile, and more productive. And we want to continue that growth. Some folks would also add that cost reduction is part of the roadmap. And don’t get me wrong — I’m not minimizing its importance, but saving costs is really a by-product and result of the four efforts I just mentioned. The bottom line is that our continued success and growth ,and inherently cost reductions, come down to efficiency, accuracy, and repeatability.
Without giving away too many secrets, we’ve got some exciting endeavors in the pipeline:
- Automation enhancements: we are working on the aforementioned enhancements to Assurant Vision Tunnel, which will be significant in their impact.
- State-of-the-art technology for box picking, cutting, and de-cartoning using machine learning and vision-driven automation.
- Further enrichments in our automated technology to broaden our applications in autonomous mobile robots (AMR) technology, automated sort and retrieval (ASRS) systems for our pre-pack areas, and AMR and sortation systems for our outbound dock areas.
Q: What’s the endgame?
Much like all the Infinity Stones that Thanos got hold of, our automation endgame is multifaceted.
Here are the top reasons why we’re leveling up in the automation game and why it’s so important to keep evolving in this space.
- Better customer experience: Faster turnaround times and improved service quality enhance the experience for our partners’ customers, leading to higher customer satisfaction and loyalty.
- Revenue growth: Empowers us to turn our reverse logistics process into a revenue stream by reselling legacy devices at the highest possible value and giving devices a second life in less than 48 hours
- Reduced environmental impact: Efficient refurbishment processes can extend the lifespan of mobile devices, reducing electronic waste and contributing to our sustainability goals.
The benefits to automation include cost savings, faster service, enhanced quality control, scalability, and improved customer satisfaction. This ultimately leads to increased revenue and a more sustainable business model, which is our major endgame.